Concrete wall making machine is a kind of mechanical equipment used to produce concrete wall panels.
Structural composition
Raw material processing system: responsible for measuring, crushing, screening and mixing raw materials such as ceramsite, cement, sand, etc., to ensure the uniformity and consistency of raw materials and provide qualified materials for subsequent mixing processes. For example, precise metering devices can accurately weigh various raw materials according to the set proportion to ensure the quality of wall panels.Mixing system: The processed raw materials are sent into the mixer, and after adding appropriate amounts of water and additives such as foaming agents, they are fully mixed to form a uniform concrete slurry. The performance of the mixer directly affects the quality of concrete. An efficient mixer can fully mix various materials to avoid uneven mixing.
Molding system: The mixed concrete slurry is injected into the mold, and it is vibrated or pressed to make it tightly fill the mold and form the desired shape and size. The precision and stability of the molding system are crucial to the appearance size and quality of the wall panels. For example, the use of advanced vibration technology can make the internal structure of the wall panels more compact.
Curing system: The formed wall panels need to be cured in the curing system, usually through high-pressure steam curing and other methods to accelerate the hydration reaction of cement and improve the strength and durability of the wall panels. The curing time, temperature and humidity and other conditions need to be strictly controlled to ensure that the performance of the wall panels meets the design requirements.
Cutting and packaging system: After the curing is completed, the wall panels are cut into predetermined sizes and shapes by cutting equipment to meet the requirements of construction. Then they are packaged for transportation and storage.
Working principle:
The working principles of different types of Concrete wall making machine may vary, but in general, various raw materials are mixed and stirred into concrete slurry in a certain proportion, and then formed in a mold, and finally made into concrete wall panels after curing and cutting processes. For example, for some lightweight concrete wall panel machines, foaming technology may be used to introduce bubbles into the concrete slurry to reduce the density of the wall panels and improve their thermal insulation performance.
Classification by wall panel material:
Ordinary Concrete wall making machine: The wall panels produced are mainly made of ordinary concrete, with high strength and stability, suitable for building structures with high strength requirements, such as load-bearing walls, basement wall panels, etc.
Lightweight concrete wall panel machine: Use lightweight aggregates (such as ceramsite, polystyrene particles, etc.) to replace part or all of the ordinary aggregates. The wall panels produced are light in weight and have good thermal insulation performance. They are often used in non-load-bearing partition walls, exterior wall insulation and other parts.
Fiber-reinforced Concrete wall making machine: Add fiber materials (such as glass fiber, carbon fiber, etc.) to concrete to enhance the tensile strength and toughness of the wall panels, improve their crack resistance and durability, and can be used in some special building parts with high durability requirements.
Classification by production process:
Vertical mold forming Concrete wall making machine: The mold is placed upright, and the concrete slurry is injected from the top of the mold and formed under the action of gravity and vibration. This production process has high production efficiency, is suitable for large-scale production, and has good dimensional accuracy and surface flatness of the wall panels.
Flat die forming wall panel machine: The mold is placed horizontally, the concrete slurry is spread on the mold, and then it is formed by pressing or vibration. The equipment structure of the flat die forming wall panel machine is relatively simple, and the operation and maintenance are relatively convenient, but the production efficiency may be relatively low. It is suitable for some small production enterprises or special-shaped wall panel production.
Advantages:
High production efficiency: It can realize automated or semi-automated production, greatly improve the production speed of wall panels, and meet the large demand for wall panels in construction projects. For example, an advanced concrete wall panel production line can produce hundreds or even thousands of square meters of wall panels per day.
Stable product quality: Through precise metering and control technology, the consistency of raw material ratio and production process of each wall panel is guaranteed, so that the product quality is more stable and reliable.
Labor saving: The automated production process reduces the links of manual operation, reduces the labor intensity of workers, and also reduces dependence on labor, saving labor costs.
Energy saving and environmental protection: Compared with traditional brick wall construction, the consumption of raw materials can be better controlled in the production process of concrete wall panels, reducing waste. At the same time, some new concrete wall panel machines adopt energy-saving technology to reduce energy consumption.
Convenient construction: Concrete wall panels are prefabricated components and can be directly installed at the construction site, which reduces the workload of wet work on site, shortens the construction period, and improves construction efficiency
Application scenarios:
Residential buildings: used to build internal and external partitions, non-load-bearing walls, etc. of residential buildings, which can meet the requirements of residential buildings for insulation, sound insulation, fire prevention and other performances.
Commercial buildings: such as partitions, firewalls, decorative wall panels and other parts in buildings such as shopping malls, office buildings, and hotels. The high strength, durability and aesthetics of concrete wall panels can meet the use needs of commercial buildings.
Industrial buildings: In industrial plants, warehouses and other buildings, concrete wall panels can be used as enclosure structures, with good wind resistance, earthquake resistance, corrosion resistance and other properties, and can adapt to the special environment of industrial buildings.
Public buildings: In public buildings such as schools, hospitals, and gymnasiums, concrete wall panels can be used for partitions, partitions, exterior walls and other parts to provide people with a safe and comfortable use environment.
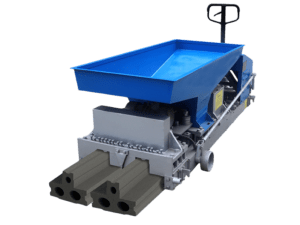